Team TREK captain Robert Bulaga and fellow engineer Jose Fierro are the first to admit they’re no spring chickens in the world of aviation. Both professional pilots, each has over 30 years of experience not only flying aircraft but also designing them. Today, however, they are focused on a new, emerging class of devices—personal flyers.
Up until recently, Bulaga and Fierro have been at the helm of TREK Aerospace, an aviation company famous for manufacturing and selling ducted propellers, which dramatically improve the efficiency of free propellers . But three years ago, TREK decided that building a personal flyer was the best way to showcase their innovative technology, and the FlyKart 1 was born.
“It was so ugly that only an engineer would love it,” Fierro recalls, “but it was fully functional and really showcased our capabilities.” Still, there was room to do more. When Fierro and Bulaga heard about the GoFly Prize from former NASA engineer Mark Moore, they saw the competition’s strict requirements as an opportunity to create a better vehicle that would meet market demand for a small, quiet, safe, and reliable personal flyer.
Throughout the first two phases of the competition, TREK developed a prototype, the FlyKart 2, a more user-friendly flyer. They are on track to complete the full-scale, manned version by the end of the summer. With no fancy testing facilities or big team to rely on, Bulaga and Fierro are determined to take their garage-built device to the Final Fly-Off.
TREK Technology at Work
Bulaga and Fierro met when Fierro was still at UC Berkeley, working towards his MBA. Mark Moore, then with NASA, recommended that Fierro meet Bulaga based on his interest in ducted propellers, noting that “Rob knows more about ducted propellers than anyone else in the world.” From there, a lifelong partnership formed. Today, the two mesh well as a team because of their diverse backgrounds. Bulaga is an aerodynamicist with experience analyzing, designing, and building unconventional aircraft, while Fierro has degrees in electrical engineering and business and is a former Marine F/A-18 pilot .
“I’m a dreamer, believing that we can do anything. Jose is more of a realist, pointing out that we can’t do everything. It’s a good balance,” Bulaga says.
Unlike several of the teams competing in the GoFly Prize, TREK is already relatively well known in the world of aviation. NASA engineers, for example, frequently ask for Bulaga’s input on their ducted propeller technology.
“Anyone that uses ducted propellers eventually comes to us,” according to Bulaga. One of the team’s earlier aircraft was featured in the film Agent Cody Banks. TREK has also consulted and partnered with large and small companies alike, working on dozens of ducted propeller projects.
“We’ve made a real difference in the area where we operate,” Fierro says, “and we’ll continue to thrive in environments where this critical use is applicable.”
Finding Balance and Forging Ahead
Today, of course, TREK is applying its ducted propeller technology to the next iteration of their personal flying device, the FlyKart 2, which they plan to submit as part of the next phase of the GoFly Prize. As a fully-operational company, TREK contends with a challenge that many other teams don’t face—a roster of customers and incoming orders to keep up with while working on their device. “I need to remind [Bulaga] sometimes that we need to work on other projects as well,” Fierro jokes.
Still, the two have managed to prioritize improvements to the FlyKart 2, experimenting with new batteries, introducing a lighter airframe and continually perfecting the application of their ducted propellers. Since TREK’s first electric drone over a decade ago, progress in battery technology has improved what is possible, which is critical because electricity as a power source typically limits device endurance and flight time. And of course, their famed ducted propellers improved the FlyKart’s endurance as well.
“To produce the same thrust, our ducted propellers use only half the power of a similarly-sized, conventional propeller. The key point is that rather than waiting for energy density of batteries to improve even further, we’re already solving the endurance challenge,” Bulaga explains. He points out that ducts provide additional advantages—being shrouded, the spinning props are inherently quieter and safer.
As the team continues to progress through Phase III, Bulaga and Fierro look forward to spending more time testing their device, and plan to make additional enhancements to the FlyKart 2. They want to, for instance, redesign the airframe to be lighter and more energy-efficient as well as add more safety features.
“It’s natural for people to wonder about the safety and reliability of these devices, but safety is paramount to us. We want people to feel secure when operating these. At the end of the day, the only thing that will change people’s mind is proof so that’s our top priority,” Fierro says.
“We expect to be flying the improved FlyKart 2 this summer. Keep an eye out for us,” Bulaga adds.
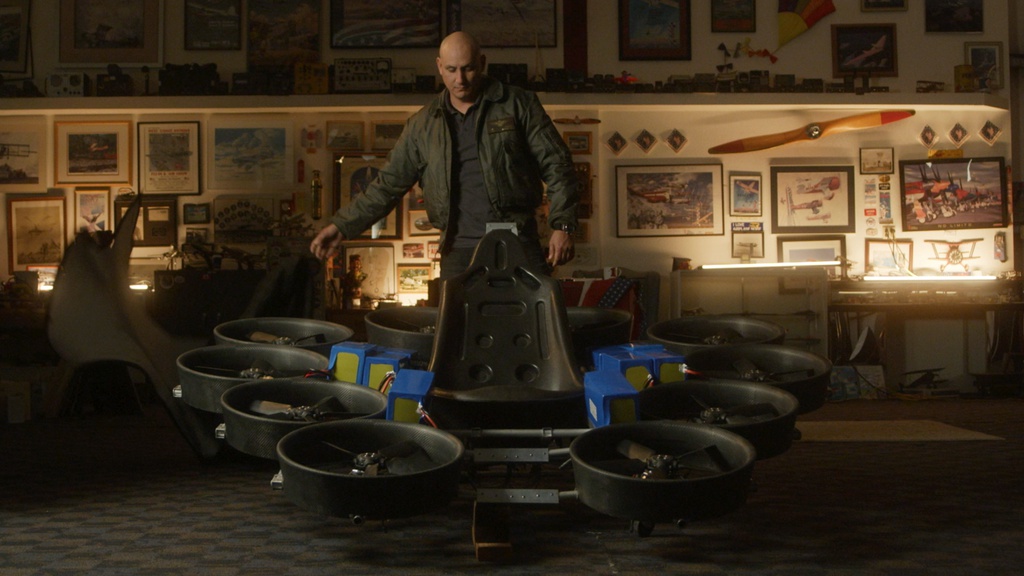